Project
Description
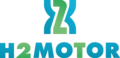
Project Objectives
Activity Plan
The first activity involves the detailed definition of the fundamental characteristics of the engine and design constraints, based on previous experience and preliminary simplified calculations.
Once the most promising configuration has been identified, accurate 1D and 3D CFD simulation models will be constructed. These models will optimize all the main geometric and functional parameters of the engine. The methodology includes the synergistic use of various state-of-the-art CAE tools, allowing for increasingly precise analysis of charge exchange and combustion processes, as well as an initial prediction of performance and pollutant emissions.
After completing the optimization phase of the "digital twin," a 3D CAD model of the entire engine will be constructed, along with the detailed design of the individual prototype components.
This will be followed by the physical realization of the prototype, its assembly, and installation at the CNR-STEMS engine test facility.
Finally, experimental tests will be conducted for the calibration and measurement of the engine's performance and emissions, demonstrating the potential of this innovative technology to reduce the environmental impact in industrial sectors and beyond.